As the textile industry develops towards personalization, environmental protection and efficient production, digital printing technology is gradually replacing traditional printing processes. Digital printing can not only achieve high-precision pattern output, but also reduce water consumption and pollution, which is in line with the trend of sustainable development. However, to ensure bright colors, uniform penetration and excellent fastness, the selection and use of textile chemical auxiliaries are crucial.
Process and Challenges of Digital Printing
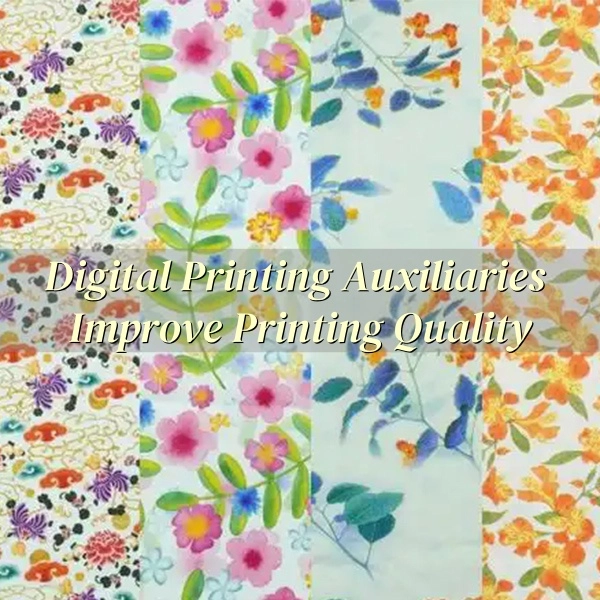
Digital printing is the use of computer-controlled inkjet technology to spray dyes directly onto the surface of fabrics, and form a lasting color effect through thermal or chemical fixation. Digital printing is suitable for various fabrics such as natural fibers, chemical fibers, and blends. However, the following challenges are still faced during the application process:
Insufficient permeability: It is difficult for dyes to fully penetrate the fabric, affecting the color consistency of the front and back.
Color fastness problems: Colors may fade or fade after washing and rubbing.
Surface uniformity: Fabrics of different fiber materials may cause uneven color absorption.
To solve these problems, textile chemical auxiliaries play a key role.
Key Roles of Textile Chemical Auxiliaries
Pretreatment Auxiliaries
In the pre-printing stage, the use of appropriate additives can improve the ink absorption and color performance of fabrics.
- Degreasing agent: removes oil and impurities on the surface of the fabric and improves the adsorption capacity of ink.
- Wetting agent: enhances the permeability of ink to the fabric and makes the dye more evenly distributed.
- Thickener: increases the residence time of ink on the fabric, reduces diffusion, and improves the clarity of the pattern.
- Adhesive: improves the adhesion of dyes or pigments and reduces uneven absorption caused by fabric characteristics.
Dyeing Auxiliaries
Dyeing auxiliaries can enhance the uniformity and color stability of dyes during digital printing, ensuring the high-quality presentation of the final pattern.
- Sequester: effectively removes metal ions, prevents color difference and precipitation during dyeing, and improves dyeing uniformity.
- Anti Creasing: reduces the wrinkles of fabrics during dyeing and improves the flatness of the finished fabric.
- Disperse & Leveling Agent: Improve the diffusion of dyes on fabrics, prevent color spots and stripes, and ensure uniform and stable colors.
Fixing and Finishing Auxiliaries
The fixing and finishing process after printing determines the durability and comfort of the final product.
- Fixing agent: Improve color fastness and prevent dye from falling off due to washing or friction.
- Softener: Improve the feel of fabrics and make printed fabrics softer and more comfortable.
- Antifouling agent: Enhance the antifouling property of fabrics and reduce the risk of contamination of printed patterns.
Bluelake Textile Chemicals Solutions
We provide a range of high-performance textile chemical auxiliaries covering the entire digital printing process, from pre-treatment, and printing to finishing, to help your products achieve higher quality.
If you are looking for textile chemical auxiliaries to optimize the digital printing process, please contact us, our professional team will provide you with customized solutions!